Before you launch your next Lean Six Sigma project, ask yourself one critical question: Is the process stable?
In our latest article, we break down why process stability is essential before pursuing any performance improvements — and what it really means for a process to be “in control.” From control charts to real-world industry examples, we’ll show you how to recognize (and achieve) stability so your Lean Six Sigma efforts don’t waste time chasing unpredictable problems.
In our second article on the DMAIC methodology, we shared practical guidance on mastering the Define and Measure phases. One of the key takeaways was:
Ensure process stability before attempting improvements.
Building on that foundation, this article aims to clarify what a stable process is, why it matters, and how to stabilize it — so it can become a viable candidate for a Lean Six Sigma (LSS) improvement project.
Stability does not imply good performance — only that the process behaves consistently and predictably over time
• Control limits are typically set at ±3σ (99.73% confidence), and if the process stays within those with no unusual patterns (runs, trends, cycles), it is statistically stable.
• Performance capability relates to specification limits, while stability relates to control limits.
What Is a Stable Process in the Lean Six Sigma Context?
A stable process operates consistently over time, showing only common-cause variation — the natural variation inherent in any process. In statistical terms, a stable process is in control, with no special-cause variation (unexpected deviations due to anomalies like machine malfunctions or human error). This common cause variation is inherent to the system, and can consequently be worked upon
A stable process is not necessarily a good process. It may consistently perform poorly — but that poor performance is predictable and can be reliably measured
Key Characteristics:
• Data points remain within control limits (typically ±3σ).
• No unusual trends, cycles, or patterns appear in control charts.
• Output is predictable, even if not within desired specification limits.
• Stability refers to statistical control, not to meeting customer requirements.
Example 1 Stable Process
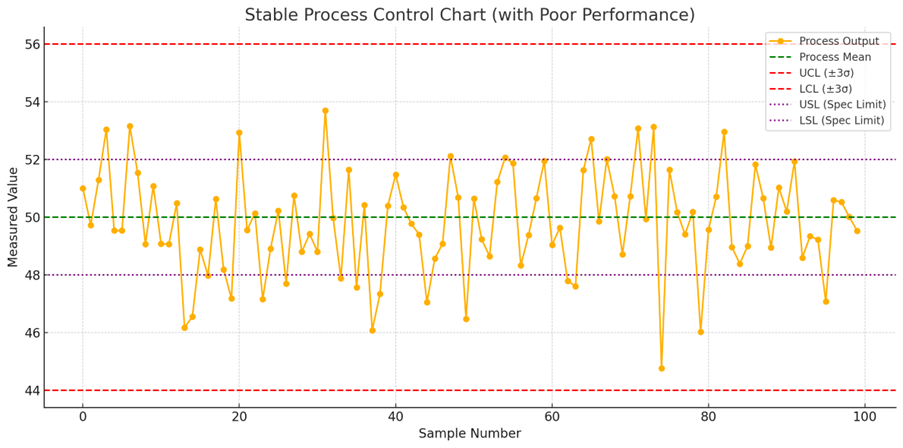
This control chart shows a stable process: all points fall within the control limits (±3σ), and there’s no pattern suggesting special causes. However, many points are near or beyond the specification limits (purple lines), showing that the process is stable but not capable — it’s consistently underperforming.
Example 2 unstable process
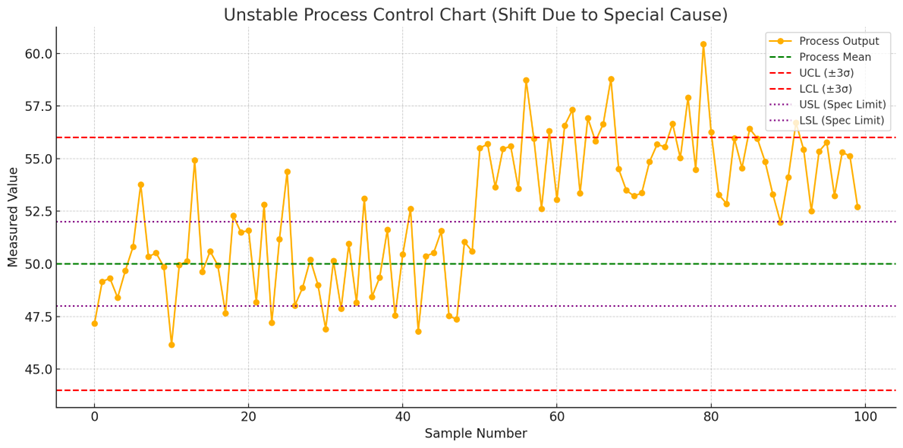
This second chart illustrates an unstable process:
• The first half of the data stays within control limits, indicating stability.
• In the second half, there’s a noticeable mean shift, with many points approaching or exceeding the upper control limit — a clear sign of special-cause variation.
• Even if some values are within specification limits, the process is not predictable over time, which makes it unstable.
In short:
• Stable but incapable = predictable but poorly performing, not meeting customer specifications.
• Unstable = unpredictable and not in control, regardless of current performance.
In Lean Six Sigma, a stable process is a prerequisite for improvement efforts—you can’t effectively reduce variation or waste unless the process is predictable.
Summary: What Defines a Stable Process?
• Output is consistent over time, even if performance is poor, not meeting customer expectations.
• Control charts show no trends, shifts, or anomalies.
• Only common-cause variation is present.
• Special causes (unexpected or assignable variations) are eliminated or under control (root cause is understood and exceptional).
Examples in Industry:
- Manufacturing:
A CNC (Computer Numerical Control) machining center producing parts with consistent dimensions.
An assembly line producing 100 units per hour with consistent defect rates.
- Healthcare:
A hospital lab processing blood tests with consistent turnaround times.
A patient intake process where forms are completed and submitted consistently within 5 minutes.
- Logistics/Warehousing:
A stable pick-and-pack process where orders are shipped within a standard time window.
Truck arrivals and departures following a predictable schedule with minimal delays.
- Financial Services:
A loan approval process where review times are consistent across applications.
Payroll processing that meets deadlines and accuracy rates every cycle.
- IT/Software:
A code deployment process that consistently takes the same amount of time with minimal bugs.
Helpdesk ticket resolution that follow a predictable lead time
Why Stability Matters in Lean Six Sigma
Both Lean (focused on waste reduction) and Six Sigma (focused on variation reduction) rely on a stable foundation:
• Improvements can’t be measured accurately in unstable processes.
• Root cause analysis becomes unreliable when variation is unpredictable.
• Sustainability of improvement gains is impossible without stability.
In a nutshell, there is no point in changing fundamentally a system that is not predictable: any attempts to apply Lean Six Sigma techniques to an unstable process may be ineffective or even counterproductive.
As a result how to Improve a Process to Make It Stable
To be a candidate for Lean Six Sigma (especially for a Green Belt project), the process must be statistically stable, meaning it only shows common-cause variation. Here’s a structured path to get there applying the DMAIC methodology (Define, Measure, Analyze, Improve, Control).
Step-by-Step Guide:
1. Define the Process
• Document inputs, outputs, and process flow.
• Identify critical-to-quality (CTQ) factors.
2. Measure the Current State
• Use tools like flowcharts, value stream maps.
• Collect baseline data (cycle time, defect rate, etc.).
3. Monitor with Control Charts
• Apply statistical process control (SPC) charts to visualize variation.
• Determine if special-cause variation exists.
4. Identify and Eliminate Special Causes
• Use Root Cause Analysis (e.g., 5 Whys, Fishbone diagram, pareto charts, cause-and-effect diagrams)
• Remove or mitigate factors causing instability (e.g., operator errors, machine issues).
5. Standardize the Process
• Implement Standard Operating Procedures (SOPs).
• Train all operators consistently.
6. Establish Monitoring and Response Plans
• Use visual management and control plans.
• Define what to do if variation occurs.
Example Green Belt Project Ideas
Manufacturing: CNC Machining Center
Project: “Stabilizing Dimensional Accuracy in CNC Machining for High-Volume Components”
• Goal: Identify causes of dimensional variation; implement tool calibration and SOPs.
• DMAIC Focus: Improve repeatability through machine maintenance, tool wear analysis, and operator training.
Healthcare: Patient Intake Process
Project: “Reducing Variation in Patient Intake Completion Times”
• Goal: Ensure all forms are completed within 5 minutes.
• DMAIC Focus: Simplify form design, improve staff workflows, and introduce digital intake.
Logistics/Warehousing: Pick-and-Pack Process
Project: “Standardizing Pick-and-Pack Times to Improve Order Accuracy and Timeliness”
• Goal: Ship all orders within a consistent time window.
• DMAIC Focus: Layout optimization, pick list design, and barcode scanning validation.
Financial Services: Loan Approval Process
Project: “Reducing Turnaround Time Variation in Loan Approvals”
• Goal: Achieve consistent review durations.
• DMAIC Focus: Standardize documentation, automate initial screening, and load balance reviews.
IT/Software: Code Deployment Process
Project: “Stabilizing Deployment Durations and Reducing Post-Release Bugs”
• Goal: Ensure consistent deploy times with minimal issues.
• DMAIC Focus: Automate deployment scripts, version control enforcement, and test coverage.
Conclusion: Stability First — Then Capability and Performance
Before a process can be improved through Lean Six Sigma, it must first be made stable — predictable, controlled, and repeatable. Only then can improvement efforts be effective and sustainable.
The good news? Process stability can be achieved — and even unreliable or inconsistent processes can become stable candidates for LSS through ad hoc improvement projects using the Green Belt-level DMAIC approach.
Stabilizing a process isn’t just a prerequisite — it’s a powerful first project on your Lean Six Sigma journey, and the foundation for successful and lasting process improvement