Avant de lancer votre prochain projet Lean Six Sigma, posez-vous une question essentielle : le processus est-il stable ?
Dans notre dernier article, nous expliquons pourquoi la stabilité des processus est essentielle avant de chercher à améliorer les performances – et ce que signifie réellement qu’un processus est « sous contrôle ». Des cartes de contrôle aux exemples concrets du secteur, nous vous montrerons comment reconnaître (et atteindre) la stabilité afin que vos efforts Lean Six Sigma ne gaspillent pas de temps à poursuivre des problèmes imprévisibles.
Pourquoi la stabilité des processus est une condition préalable aux projets Lean Six Sigma
Dans notre deuxième article sur la méthodologie DMAIC, nous avons partagé des conseils pratiques pour maîtriser les phases Définir et Mesurer. L’un des principaux points à retenir était le suivant :
Assurer la stabilité du processus avant de tenter des améliorations.
S’appuyant sur ces bases, cet article vise à clarifier ce qu’est un processus stable, pourquoi il est important et comment le stabiliser – afin qu’il puisse devenir un candidat viable pour un projet d’amélioration Lean Six Sigma (LSS).
La stabilité n’implique pas de bonnes performances – seulement que le processus se comporte de manière cohérente et prévisible dans le temps.
• Les limites de contrôle sont généralement fixées à ±3σ (confiance de 99,73 %), et si le processus reste dans ces limites sans schémas inhabituels (séries, tendances, cycles), il est statistiquement stable.
• La capacité de performance est liée aux limites de spécification, tandis que la stabilité est liée aux limites de contrôle.
Qu’est-ce qu’un processus stable dans le contexte Lean Six Sigma ?
Un processus stable fonctionne de manière cohérente dans le temps, ne présentant que des variations de cause commune – la variation naturelle inhérente à tout processus. En termes statistiques, un processus stable est sous contrôle, sans variation de cause spéciale (écarts inattendus dus à des anomalies telles que des dysfonctionnements de machine ou des erreurs humaines). Cette variation de cause commune est inhérente au système et peut donc être corrigée.
Un processus stable n’est pas nécessairement un bon processus. Il peut systématiquement être peu performant – mais cette mauvaise performance est prévisible et peut être mesurée de manière fiable.
Caractéristiques clés :
• Les points de données restent dans les limites de contrôle (généralement ±3σ).
• Aucune tendance, cycle ou schéma inhabituel n’apparaît dans les cartes de contrôle.
• Le résultat est prévisible, même s’il ne se situe pas dans les limites de spécification souhaitées.
• La stabilité se réfère au contrôle statistique, et non à la satisfaction des exigences du client.
Exemple 1 : Processus stable
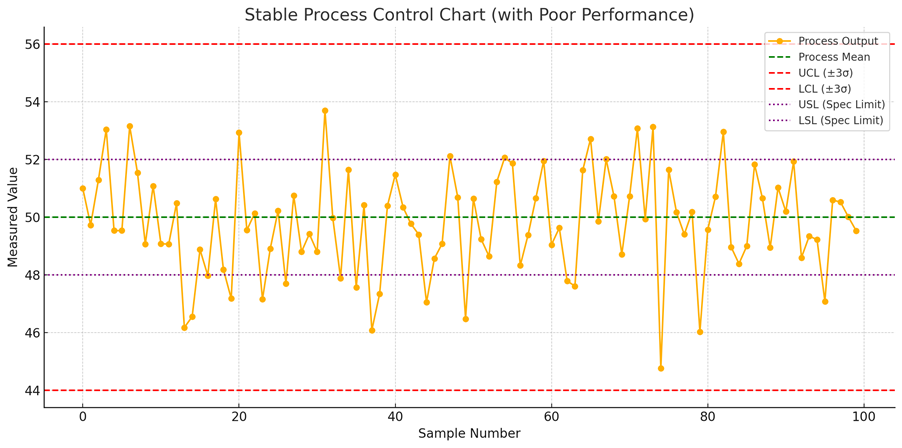
Cette carte de contrôle montre un processus stable : tous les points se situent dans les limites de contrôle (±3σ) et il n’y a aucun schéma suggérant des causes spéciales. Cependant, de nombreux points sont proches ou au-delà des limites de spécification (lignes violettes), ce qui montre que le processus est stable mais pas capable : il est systématiquement sous-performant.
Exemple 2 : Processus instable
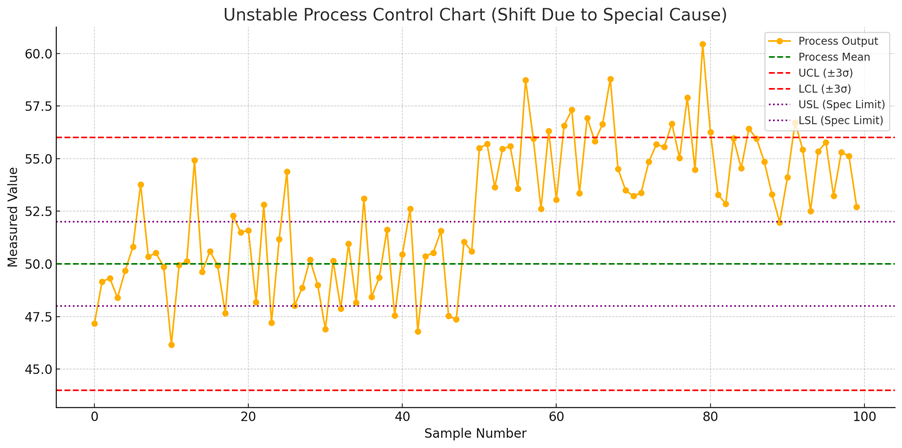
Cette deuxième carte illustre un processus instable :
• La première moitié des données reste dans les limites de contrôle, ce qui indique une stabilité.
• Dans la seconde moitié, on observe un décalage notable de la moyenne, de nombreux points approchant ou dépassant la limite de contrôle supérieure – ce qui est un signe évident d’une variation de cause spéciale.
• Même si certaines valeurs se situent dans les limites de spécification, le processus n’est pas prévisible dans le temps, ce qui le rend instable.
En bref :
• Stable mais incapable = prévisible mais peu performant, ne répondant pas aux spécifications du client.
• Instable = imprévisible et non maîtrisé, quelles que soient les performances actuelles.
Dans Lean Six Sigma, un processus stable est une condition préalable aux efforts d’amélioration – vous ne pouvez pas réduire efficacement la variation ou le gaspillage si le processus n’est pas prévisible.
Résumé : Qu’est-ce qui définit un processus stable ?
• Le résultat est cohérent dans le temps, même si les performances sont médiocres et ne répondent pas aux attentes du client.
• Les cartes de contrôle ne montrent aucune tendance, aucun décalage ni aucune anomalie.
• Seule la variation de cause commune est présente.
• Les causes spéciales (variations inattendues ou attribuables) sont éliminées ou maîtrisées (la cause première est comprise et exceptionnelle).
Exemples dans l’industrie :
Fabrication :
• Un centre d’usinage CNC (Computer Numerical Control) produisant des pièces avec des dimensions cohérentes.
• Une ligne d’assemblage produisant 100 unités par heure avec des taux de défauts constants.
Santé :
• Un laboratoire hospitalier traitant des analyses de sang avec des délais d’exécution constants.
• Un processus d’admission des patients où les formulaires sont remplis et soumis de manière cohérente en moins de 5 minutes.
Logistique/Entreposage :
• Un processus de prélèvement et d’emballage stable où les commandes sont expédiées dans un délai standard.
• Arrivées et départs de camions suivant un calendrier prévisible avec un minimum de retards.
Services financiers :
• Un processus d’approbation de prêt où les délais d’examen sont constants pour toutes les demandes.
• Traitement de la paie respectant les délais et les taux d’exactitude à chaque cycle.
Informatique/Logiciel :
• Un processus de déploiement de code qui prend systématiquement le même temps avec un minimum de bogues.
• Résolution des tickets d’assistance technique suivant un délai prévisible.
Pourquoi la stabilité est-elle importante dans Lean Six Sigma ?
Le Lean (axé sur la réduction des déchets) et le Six Sigma (axé sur la réduction des variations) reposent tous deux sur une base stable :
• Les améliorations ne peuvent pas être mesurées avec précision dans les processus instables.
• L’analyse des causes premières devient peu fiable lorsque la variation est imprévisible.
• La pérennité des gains d’amélioration est impossible sans stabilité.
En bref, il ne sert à rien de modifier fondamentalement un système qui n’est pas prévisible : toute tentative d’application des techniques Lean Six Sigma à un processus instable risque d’être inefficace, voire contre-productive.
Par conséquent, comment améliorer un processus pour le rendre stable ?
Pour être candidat au Lean Six Sigma (en particulier pour un projet Green Belt), le processus doit être statistiquement stable – ce qui signifie qu’il ne présente que des variations de cause commune. Voici un chemin structuré pour y parvenir en appliquant la méthodologie DMAIC (Définir, Mesurer, Analyser, Améliorer, Contrôler).
Guide étape par étape :
1. Définir le processus
* Documenter les entrées, les sorties et le flux du processus.
* Identifier les facteurs critiques pour la qualité (CTQ).
2. Mesurer l’état actuel
* Utiliser des outils tels que les organigrammes, les cartes de chaîne de valeur.
* Recueillir des données de référence (temps de cycle, taux de défauts, etc.).
3. Surveiller avec des cartes de contrôle
* Appliquer les cartes de contrôle statistique des processus (SPC) pour visualiser la variation.
* Déterminer s’il existe une variation de cause spéciale.
4. Identifier et éliminer les causes spéciales
* Utiliser l’analyse des causes premières (par exemple, les 5 Pourquoi, le diagramme d’Ishikawa, les diagrammes de Pareto, les diagrammes de causes et effets).
* Supprimer ou atténuer les facteurs qui causent l’instabilité (par exemple, les erreurs de l’opérateur, les problèmes de la machine).
5. Normaliser le processus
* Mettre en œuvre des procédures opérationnelles standard (POS).
* Former tous les opérateurs de manière cohérente.
6. Établir des plans de surveillance et de réponse
* Utiliser la gestion visuelle et les plans de contrôle.
* Définir ce qu’il faut faire en cas de variation.
Exemples d’idées de projets Green Belt
Fabrication : Centre d’usinage CNC
• Projet : « Stabiliser la précision dimensionnelle dans l’usinage CNC pour les composants à grand volume »
• Objectif : Identifier les causes de la variation dimensionnelle ; mettre en œuvre l’étalonnage des outils et les POS.
• Orientation DMAIC : Améliorer la répétabilité grâce à la maintenance des machines, à l’analyse de l’usure des outils et à la formation des opérateurs.
Santé : Processus d’admission des patients
• Projet : « Réduire la variation des temps de remplissage des formulaires d’admission des patients »
• Objectif : S’assurer que tous les formulaires sont remplis en moins de 5 minutes.
• Orientation DMAIC : Simplifier la conception des formulaires, améliorer les flux de travail du personnel et introduire l’admission numérique.
Logistique/Entreposage : Processus de prélèvement et d’emballage
• Projet : « Normaliser les temps de prélèvement et d’emballage afin d’améliorer la précision et la rapidité des commandes »
• Objectif : Expédier toutes les commandes dans un délai cohérent.
• Orientation DMAIC : Optimisation de l’aménagement, conception des listes de prélèvement et validation de la lecture des codes-barres.
Services financiers : Processus d’approbation de prêt
• Projet : « Réduire la variation du délai d’exécution des approbations de prêt »
• Objectif : Obtenir des durées d’examen cohérentes.
• Orientation DMAIC : Normaliser la documentation, automatiser le dépistage initial et équilibrer la charge des examens.
Informatique/Logiciel : Processus de déploiement de code
• Projet : « Stabiliser les durées de déploiement et réduire les bogues après la publication »
• Objectif : Assurer des temps de déploiement cohérents avec un minimum de problèmes.
• Orientation DMAIC : Automatiser les scripts de déploiement, appliquer le contrôle des versions et assurer la couverture des tests.
Conclusion : La stabilité d’abord – puis la capacité et la performance
Avant qu’un processus puisse être amélioré grâce à Lean Six Sigma, il doit d’abord être stabilisé – c’est-à-dire rendu prévisible, maîtrisé et reproductible. Ce n’est qu’alors que les efforts d’amélioration peuvent être efficaces et durables.
La bonne nouvelle ? La stabilité des processus peut être atteinte – et même les processus peu fiables ou incohérents peuvent devenir des candidats stables pour le LSS grâce à des projets d’amélioration ponctuels utilisant l’approche DMAIC de niveau Green Belt.
La stabilisation d’un processus n’est pas seulement une condition préalable – c’est un premier projet puissant dans votre parcours Lean Six Sigma, et le fondement d’une amélioration des processus réussie et durable.